The Ultimate Guide to Welding WPS Procedures: A Detailed Introduction for Welders
In the detailed globe of welding, Welding Procedure Requirements (WPS) offer as the foundation of making certain high quality, uniformity, and safety and security in welding procedures (welding WPS). As we dig into the numerous elements of a WPS and explore the complexities of certification and accreditation, we will reveal the crucial role these procedures play in the realm of welding.
Value of WPS Procedures
Recognizing the relevance of Welding Procedure Specifications (WPS) procedures is important for guaranteeing the top quality and honesty of bonded structures. WPS treatments function as a roadmap for welders, outlining the required steps, parameters, and materials called for to accomplish an audio weld. By sticking to WPS guidelines, welders can ensure consistency in their work, resulting in reliable and structurally sound welds.
Among the key reasons WPS procedures are necessary is their role in keeping weld quality and stability. Complying with the defined welding specifications and methods detailed in the WPS assists protect against defects such as porosity, cracking, or insufficient fusion, which can endanger the stamina and resilience of the weld. In addition, WPS treatments are essential for ensuring compliance with market standards and codes. By complying with well-known WPS standards, welders can show that their job satisfies the essential needs for security and top quality, supplying guarantee to clients, inspectors, and governing bodies. In significance, the relevance of WPS treatments can not be overstated, as they are fundamental to achieving constant, top notch welds that fulfill sector criteria and specifications.

Elements of a WPS
A Welding Treatment Spec (WPS) usually comprises vital components that information the specific requirements for performing a weld, ensuring consistency and quality in the welding procedure. The crucial components of a WPS include necessary variables such as base metals, filler metals, interpass and preheat temperature levels, welding procedures, securing gases, welding placements, and post-weld heat therapy requirements.
Base metals refer to the products being joined, while filler metals are made use of to fill the space in between the base steels throughout welding. The welding procedure lays out the details method to be made use of, whether it's gas metal arc welding (GMAW), secured metal arc welding (SMAW), or one more technique. Welding placements define the positionings in which welding can be carried out.

Qualification and Certification
Having actually developed the necessary parts of a Welding Treatment Requirements (WPS), the focus currently moves towards the important facets of credentials and qualification in welding methods.
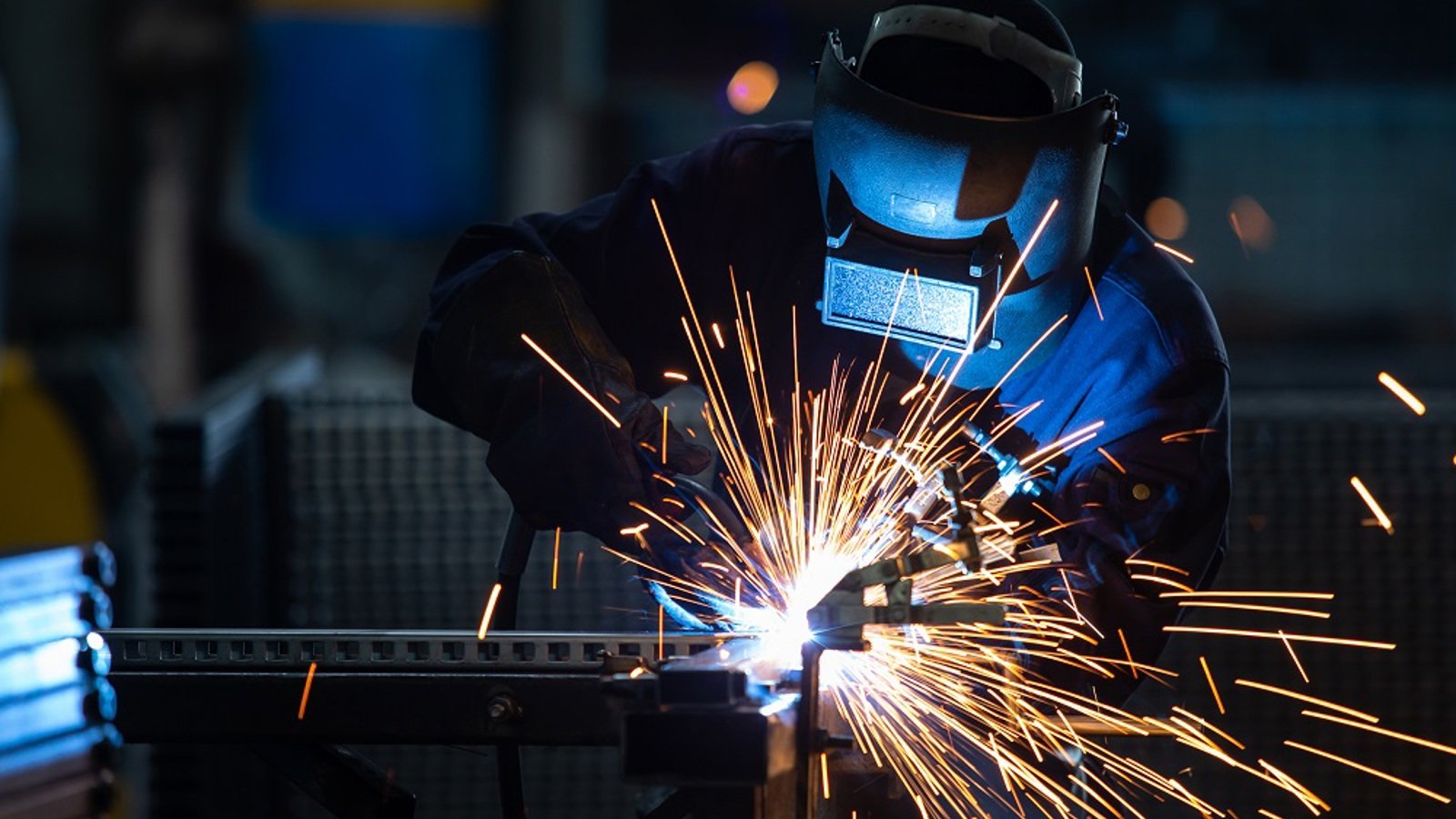
Certification, on the other hand, is the formal recognition of a welder's credentials by a pertinent certification body or organization. Welding accreditations are commonly based on the details welding procedures, products, and placements a welder is qualified to collaborate with. Holding a legitimate welding certification shows that a welder meets industry standards and is qualified to perform welding jobs to the needed specifications.
Developing a WPS
To establish a Welding Procedure Specification (WPS) that satisfies sector requirements, cautious consideration of welding procedures, products, and functional parameters is necessary. The initial step in creating a WPS is to determine the welding procedure to be utilized, such as gas steel arc welding (GMAW) or protected steel arc navigate to this website welding (SMAW)

Implementing and Checking WPS
Upon finalizing the detailed Welding Procedure Specification (WPS) that carefully information welding processes, materials, functional criteria, and quality control measures, the focus changes to successfully applying and checking the recognized treatments. Execution entails making certain that all welders involved in the task are familiar with the WPS and follow it diligently throughout the welding process. This needs giving ample training and supervision to ensure adherence to the defined procedures. Monitoring the WPS includes continual oversight to confirm that welding activities align with the documented requirements. Inspections, testing, and quality assurance measures are necessary elements of the surveillance process to identify any kind of concerns visit their website or variances without delay. Routine audits and testimonials of the welding procedures help in keeping uniformity and high quality throughout the task. Efficient application and monitoring of the WPS are essential for ensuring the honesty, strength, and safety and security of the welded joints, eventually contributing to the total success of the welding job.
Verdict
To conclude, understanding and complying with Welding Procedure Requirements (WPS) is crucial for welders to ensure top quality, consistency, and safety and security in their job. By understanding the elements of a WPS, acquiring appropriate certifications and accreditations, developing detailed procedures, and implementing and monitoring them successfully, welders can enhance their skills and proficiency in welding techniques. Abiding by WPS treatments is necessary for producing top quality welds and meeting industry standards.
In the intricate globe of welding, Welding Procedure Requirements (WPS) offer as the foundation of making sure high quality, uniformity, and security in welding procedures. The welding process lays out the certain technique to be made use of, whether it's gas steel arc welding (GMAW), protected steel arc welding (SMAW), or an additional technique.To develop a Welding Treatment Requirements (WPS) that fulfills industry standards, mindful factor Visit Your URL to consider of welding processes, products, and functional specifications is vital. The initial step in developing a WPS is to identify the welding process to be made use of, such as gas steel arc welding (GMAW) or secured metal arc welding (SMAW)Upon completing the extensive Welding Procedure Spec (WPS) that carefully information welding processes, products, functional parameters, and quality assurance procedures, the focus changes to successfully applying and checking the recognized procedures.
Comments on “Advanced Welding WPS: Tailoring Requirements for Complicated Tasks”